Автоматизированная система транспортировки для кабины К5
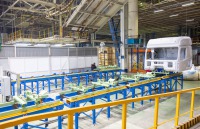
На автомобильном заводе «КАМАЗа» проходит испытание уникальная автоматизированная система транспортировки каркаса кабины автомобилей поколения К5.
Каркас кабины для большегруза премиум-класса – важный груз, к тому же путь от завода каркасов кабин (ЗКК) до автомобильного завода (АвЗ) он преодолевает с приоткрытыми дверями, что создаёт дополнительные риски.
«Простая на первый взгляд задача требовала комплексного подхода, – разъяснил директор департамента логистики перспективных кабин Рустем Хамидуллин. – Нужно было создать системы транспортировки для установки на АвЗ и в фургоне, спроектировать сам фургон и подобрать под процесс модель автомобиля. Для успешной стыковки двух систем высоту седельного тягача КАМАЗ-5490 пришлось уменьшить на 200 мм».
В реализации проекта вместе с руководителями и специалистами логистического центра участвовали конструкторы и технологи блока развития, «НЕФАЗа», а технические требования на разработку автоматической системы транспортировки передали в челнинскую компанию «Инженер».
По сценарию разгрузка длится около 20 минут: большегруз стыкуется с воротами, водитель открывает прицеп, подключается к системе, и четыре каркаса кабины на скидах медленно выезжают из кузова и перемещаются в производственный корпус.
Первым на свет появился нестандартный автомобиль. Конструкторы опустили уровень седельного устройства, доработали раму. Шасси предполагало комплектацию низкопрофильными колёсами, которые тоже были поставлены по специальному заказу. Эстафету принял «НЕФАЗ» – нестандартный прицеп для системы транспортировки должен быть шире обычного. Чтобы водителю было удобнее стыковаться, к приёмному доку будет установлена система парковки с видеокамерами и увеличен размер креплений для зеркал. Регулярные рейсы будут совершать два автомобиля с такими прицепами.
Транспортная система, обеспечивающая поставку каркасов К5, должна быть такой же высокотехнологичной, как сам большегруз премиум-класса. Электроника настроена так, что скорость конвейера внутри автомобиля и скорость конвейера, смонтированного внутри корпуса АвЗ, одинаковы. Когда каркас вкатывается в прицеп на скиде и занимает своё место, захваты системы его надёжно фиксируют. После доставки на АвЗ будущие кабины одна за другой выезжают из фургона.
«Каждая единица продукции, как и сам скид, идентифицированы RFID-метками. На них записывается номер каркаса, модель, цвет, что пока не отменяет дубликата на бумажном носителе, – рассказал начальник отдела логистических технологий Николай Аверьянов. – При прохождении через считыватель, смонтированный рядом с конвейерной системой, вся информация отправляется в систему SAP. Работник склада фиксирует приход груза на мониторе своего рабочего компьютера. Видят его и в центре управления производством «КАМАЗа». Дальше вся информация переносится на метку, которая будет крепиться уже на каркас кабины».
Для хранения каркасов определено место на стеллажах на 32 ячейки – эта зона как раз формируется работниками логистического центра. Информация о месте нахождения каркаса будет храниться в системе управления складом SAP.
Дальше его путь тоже известен – каркас поедет на конвейер сборки кабины АвЗ. Его данные пополнят электронное досье на большегруз, а один из экземпляров получит покупатель. Система может трудиться круглосуточно. В ритме конвейера она начнёт работать в 2020 году.
Категория: КАМАЗ
Дата: 14 января 2020